汽车传感器作为汽车电子控制系统的关键组成部分,承担着采集各类环境与车辆状态信息的重要职责,其工作可靠性直接关系到汽车的行驶安全与性能表现。在汽车行驶过程中,传感器往往要经历剧烈的温度变化,从寒冷冬季的 - 40℃到发动机舱附近的 125℃,这种极限温差会对传感器的精度、稳定性和使用寿命产生显著影响。两箱式冷热冲击试验箱凭借其快速温度切换能力和精准的环境模拟功能,成为评估汽车传感器耐温度冲击性能的核心设备,为汽车传感器的研发、生产和质量管控提供了坚实的技术支撑。
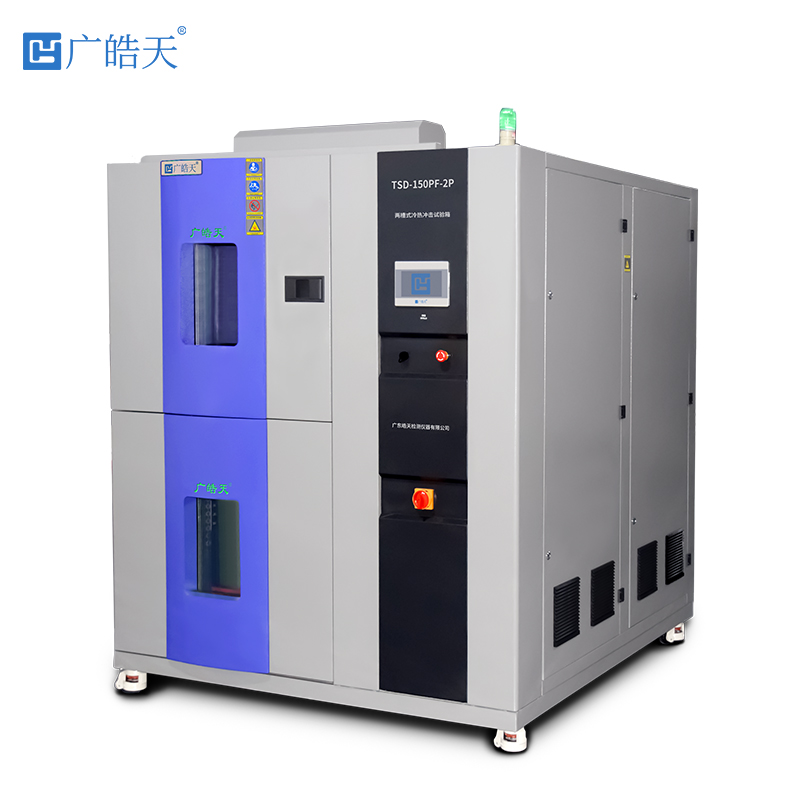
两箱式冷热冲击试验箱的测试原理与技术优势
两箱式冷热冲击试验箱主要由高温箱、低温箱和样品转移机构三部分组成,其核心测试原理是通过将汽车传感器在高温环境与低温环境之间进行快速切换,模拟传感器在实际使用中可能遭遇的极限温度冲击。高温箱通常可提供 60℃-200℃的高温环境,低温箱则能实现 - 70℃-0℃的低温条件,样品转移机构可在 10 秒内将传感器从一个箱体转移至另一个箱体,确保温度冲击的瞬间性和剧烈性,满足 IEC 60068-2-14、GB/T 2423.22 等国际和国内测试标准对温度冲击测试的严苛要求。
相较于传统的单箱式冷热冲击试验箱,两箱式设备具有显著的技术优势。首先,高温箱和低温箱独立控温,可分别精准维持设定的高温和低温,避免了单箱式设备因温度交替调节导致的能量损耗和控温精度下降问题,温度控制精度可达 ±2℃,温度均匀性在 ±3℃以内。其次,快速转移机构保证了传感器在高温与低温环境之间的切换时间极短,能最大限度地模拟真实工况下的温度突变,更准确地激发传感器内部可能存在的潜在缺陷,如材料热胀冷缩不一致导致的结构松动、焊点疲劳开裂等。此外,两箱式结构可容纳更多数量或更大尺寸的汽车传感器,支持批量测试,提高测试效率,满足汽车制造业的规模化生产需求。
汽车传感器的两箱式冷热冲击测试流程
汽车传感器种类繁多,包括温度传感器、压力传感器、加速度传感器、氧传感器等,不同类型的传感器对温度冲击的敏感程度和测试要求存在差异,但基本测试流程大致相同,主要包括测试前准备、参数设定、循环测试和结果评估四个阶段。
在测试前准备阶段,需对汽车传感器进行外观检查,确保传感器表面无破损、引脚无弯曲或氧化现象,避免因传感器本身的物理缺陷影响测试结果的准确性。随后,根据传感器的安装方式和实际工作状态,设计专用的固定夹具,将传感器牢固地安装在样品架上,保证传感器在转移过程中不会发生位移或碰撞,同时确保传感器的感测部位能够充分暴露在高低温环境中,与箱内空气充分接触,实现快速的温度交换。此外,还需连接传感器的信号输出线至外部数据采集设备,如示波器、万用表或专用的传感器测试系统,以便实时监测传感器在温度冲击过程中的输出信号变化。
参数设定是测试流程的关键环节,需根据传感器的应用场景和相关行业标准确定具体的测试参数。对于安装在发动机舱内的温度传感器和压力传感器,考虑到发动机启动和停止时的剧烈温度变化,高温设定通常为 150℃,低温设定为 - 40℃,每个温度段的保持时间为 30 分钟,温度冲击循环次数设定为 500 次,以模拟传感器在汽车使用寿命内可能经历的温度冲击总量。对于安装在车身外部的环境光传感器,高温可设定为 85℃,低温为 - 30℃,保持时间 20 分钟,循环次数 300 次。在参数设定过程中,还需对样品转移时间、箱内风速等辅助参数进行设置,一般要求转移时间≤10 秒,箱内风速保持在 1-2m/s,确保传感器能够快速达到箱内设定温度。

循环测试阶段由试验箱自动完成,设备按照设定的参数交替将传感器置于高温箱和低温箱中,并通过数据采集设备实时记录传感器的输出信号。在高温阶段,监测传感器在高温环境下的信号漂移情况,如温度传感器的测量误差是否超出允许范围;在低温阶段,观察传感器是否出现信号中断、响应延迟等现象,如加速度传感器在低温下能否准确捕捉车辆的加速度变化。测试过程中,设备会自动记录每个循环的高温保持时间、低温保持时间、温度极值等数据,形成完整的测试日志,为后续的结果评估提供依据。
测试结束后,进入结果评估阶段。首先对传感器进行外观检查,查看是否有裂纹、变形、引脚脱落等物理损伤;然后通过专业设备检测传感器的电气性能,如测量传感器的输出信号精度、响应时间、线性度等参数,并与测试前的初始参数进行对比。若传感器在 500 次温度冲击循环后,外观无明显损伤,输出信号精度变化在 ±2% 以内,响应时间变化不超过 10%,则判定该传感器通过测试,具备良好的耐温度冲击性能;反之,若出现物理损坏或性能参数超出允许范围,则需分析失败原因,可能是传感器内部封装材料选择不当、焊点工艺不合格或电路设计存在缺陷等,为传感器的改进提供方向。
两箱式冷热冲击测试对汽车传感器可靠性的提升作用
汽车传感器工作环境复杂多变,尤其是在恶劣气候条件下,如寒冷地区的冬季冷启动、高温地区的夏季暴晒后淋雨等,温度的急剧变化会对传感器的性能产生严重影响。两箱式冷热冲击试验箱通过模拟这些苛刻温度冲击场景,能够有效暴露传感器在设计、材料和制造过程中存在的潜在问题,从而推动传感器可靠性的提升。
在材料层面,温度冲击会导致传感器内部不同材料(如金属外壳、陶瓷基底、塑料封装等)因热膨胀系数差异而产生内应力,长期反复的应力作用可能引发材料疲劳、开裂。通过两箱式冷热冲击测试,可以筛选出更适合恶劣温度环境的材料组合,例如采用低膨胀系数的陶瓷材料作为传感器基底,搭配耐高温的硅胶封装,减少材料间的应力差异,提高传感器的结构稳定性。
在制造工艺方面,测试能够发现焊接、封装等工艺环节的缺陷。传感器引脚与电路板的焊点在温度冲击下容易因热胀冷缩产生疲劳,导致虚焊或脱焊,两箱式冷热冲击测试可加速这一过程,使潜在的焊点问题提前暴露。通过对测试后失效的传感器进行解剖分析,企业可以优化焊接工艺参数,如调整焊接温度、时间和焊锡量,采用回流焊代替手工焊接,提高焊点的强度和可靠性。
在设计优化上,测试数据为传感器的电路设计提供了重要参考。例如,某些压力传感器在低温冲击下会出现输出信号漂移,经分析发现是电路中的电容在低温下容量变化过大所致,工程师可根据测试结果更换低温性能更稳定的电容型号,或在电路中增加温度补偿电路,抵消温度变化对传感器输出的影响。同时,通过测试不同结构设计的传感器在温度冲击下的表现,可优化传感器的内部结构布局,如合理安排元器件的位置,避免敏感元件靠近热源或易受温度冲击的区域,提升传感器的整体耐温冲击能力。
两箱式冷热冲击试验箱作为汽车传感器可靠性测试的重要手段,其应用不仅确保了传感器在苛刻温度环境下的稳定工作,也为汽车制造业的高质量发展提供了有力保障。随着汽车智能化、电动化的不断推进,对汽车传感器的性能要求日益提高,两箱式冷热冲击试验箱将朝着更高温度范围、更快温度切换速度、更智能化的方向发展,如集成 AI 算法实现测试数据的自动分析和故障预警,进一步提升测试效率和准确性,为汽车传感器的技术创新和品质升级持续赋能。
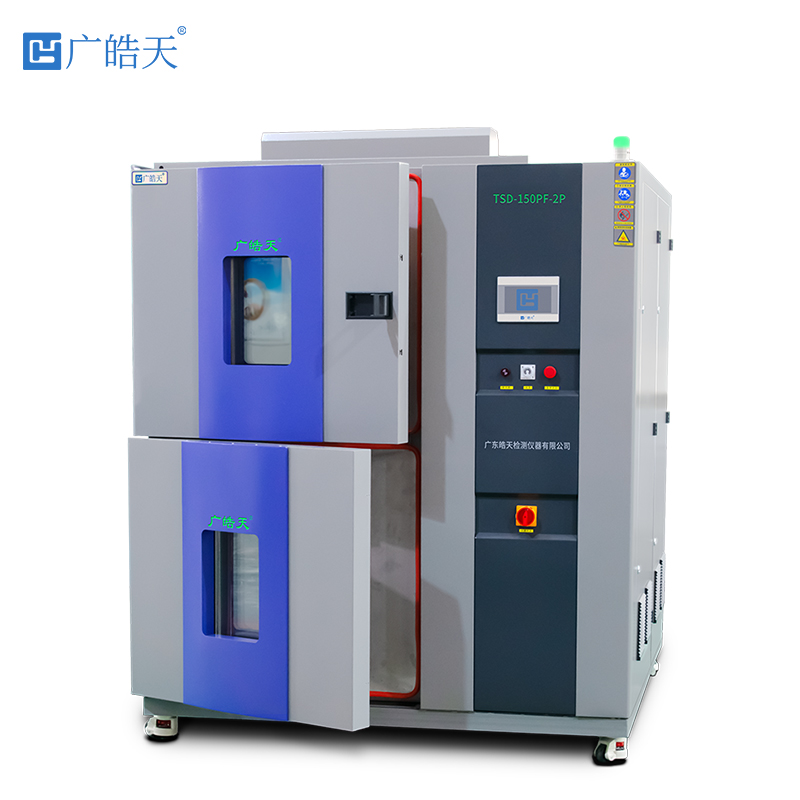